Machines for making briquettes are a crucial equipment in the energy sector. They are employed to transform waste materials into fuel for industrial, heating, and culinary activities. Although briquette machines have been around for a while, technology has advanced tremendously since then. The process of creating briquettes, the various types of briquette machines that are on the market, and the essential parts of a briquette machine will all be covered in this article.
The Creation of Briquettes
In the briquetting process, biomass or other waste materials are compressed under intense pressure to create a solid fuel. Shredding and grinding the raw materials to a uniform size is the first step in effective material preparation. To make a homogeneous mixture, the ingredients are combined with binders. Binders, which can be either natural or artificial, aid in keeping the briquette together.
Briquetting can be done with a variety of raw materials, including sawdust, rice husks, coconut shells, and coffee husks. Each material has special qualities, and the choice of material is influenced by the briquette’s intended function.
There are moist and dry techniques for adding binders to the mixture. The binders are combined with water to create a slurry, which is then added to the mixture in the wet technique. The binders are immediately added to the mixture using the dry technique in powder form. Depending on the raw material utilized and the desired properties of the briquette, the choice of binder and additional technique must be made.
Briquette-making machine parts
A pressing system, a heating system, and a cooling system are some of the vital parts of a briquette machine. To create a briquette, the raw material and binder must be compressed by the pressing mechanism. To speed up the bonding process, the mixture’s temperature is increased using the heating system. After the briquette has been created, the temperature is lowered using the cooling system to stop it from cracking.
Pressing systems come in a variety of designs, such as piston presses, screw presses, hydraulic presses, and mechanical stamping presses. Each technique is suitable for various types of raw materials and has its own distinct features.
A briquette machine’s heating system may be electric, gas, or diesel-powered. The most popular and convenient heating systems are electric ones, which are also the most energy-efficient. In places with little access to electricity, heating systems fueled by gas and diesel are frequently used.
There are two types of cooling systems: natural and forced. Allowing the briquette to cool down spontaneously after it has been created is known as natural cooling. Using fans or coolers to accelerate the cooling process is known as forced cooling. For large-scale manufacturing, forced cooling is preferable since it shortens the cooling-down period for the briquettes and can boost briquette machine output.
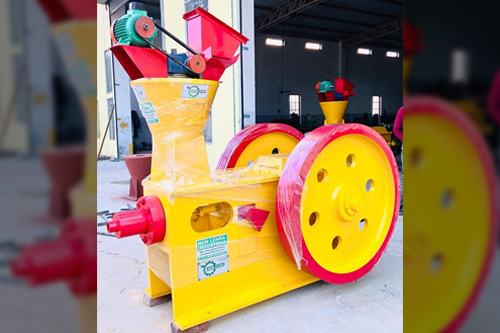
Market-available Briquette Machine Types
There are various different types of briquette machines on the market, each with certain benefits and drawbacks. The following categories of briquette makers:
- Piston Press Briquette Machines: These devices compress the raw material and binder into a briquette using a reciprocating piston. Often employed in small-scale production, piston press machines may create briquettes in a variety of shapes and sizes.
- Screw press briquette makers: These tools compress the raw material and binder into a briquette using a screw. Screw press machines can create briquettes of a consistent size and shape and are appropriate for medium- to large-scale production.
- Hydraulic press briquette machines: These devices compress the raw material and binder into a briquette using hydraulic pressure. High-density briquettes can be produced by hydraulic press machines, which are appropriate for large-scale production.
- Mechanical Stamping Briquette Machines: Devices for compressing raw materials and binders into briquettes through mechanical stamping are known as mechanical stamping briquette machines. Mechanical stamping equipment can create briquettes of various shapes and sizes and is appropriate for large-scale production.
Cost, output, and efficiency are significant considerations while selecting a briquette machine. The choice of briquette machine relies on the particular requirements of the user and each type has its own advantages and limitations.
Briquette Machine Features
Machines for making briquettes have a number of features that make them simple to operate, effective, and secure. While selecting a briquette machine, some characteristics to consider are:
- Variable Speed Drives (VSDs): VSDs let users regulate the briquette machine’s speed, which can increase productivity and lower energy use.
- Automatic Lubrication System: An automatic lubrication system makes sure that the briquette machine’s moving parts are adequately lubricated, which can increase the machine’s lifespan and lower maintenance costs.
- Integrated Control System: The functioning of the briquette machine may be monitored and controlled by users thanks to an integrated control system, which can increase productivity and lower the danger of accidents.
- Safety Features: Briquette makers are equipped with a number of safety measures, including emergency stop buttons, safety guards, and sensors. The likelihood of accidents and injuries is decreased because of these factors.
- Possibilities for Customization: Some briquette machines provide customization features, such as swappable molds or dies, that enable users to create briquettes in a variety of sizes and forms.
Conclusion
As more people explore sustainable and renewable energy sources, briquette machines are becoming an even more crucial tool in the energy sector. It is crucial to take into account features like VSDs, automatic lubrication systems, and safety features when selecting a briquette machine. Other significant considerations are the type of pressing system, heating system, and cooling system. Users may choose the best machine for their needs and create high-quality briquettes quickly and safely by studying the many types of briquette machines that are available on the market and their advantages.